Ich möchte ein neues Chassis Entwickeln das von der Konstruktionsart her auf dem alten 1.0er basiert.
Ich hoffe es finden sich einige die Interesse drauf haben und helfen.
Wir haben ja ein sehr flexibles Software/Hardware System, nur das Chassis System ist sehr unflexibel und kaum modifizierbar.
Meine Überlegung geht in Richtung eines Dualen Systems mit verschiedenen Kombinationsmöglichkeiten.
Dabei gibt es einmal die Technik/Antriebssektion und die Nutzungssektion. (Mir fällt gerade kein besseres Wort ein)
In der Technik Sektion sind die Antriebe (36/42er Getriebemotoren, Brushless/Brushed ) Akkus (1 oder 2) und die Elektronik verbaut.
Neben dem Ardumower Mainboard muss der Platz ausreichend für ein paar Extras sein. (RaspberryPI, BMS, GPS....)
Die Nutzungssektion kann an die Technik Sektion gekoppelt werden und ist je nach Wunsch in Verschiedenen Ausführungen erhältlich.
Das heißt zum Beispiel
-mit einer oder zwei Mähscheiben Ausgestattet
-mit einer Transportplattform (z.B. für eine Mörtelwanne als Elektrische Schubkarre)
-mit einem Sitz und Lenksystem als kleines Elektro-Kettcar für Kinder
-mit einer Schneewalze
-mit einem Streuwagen für Dünger
Die Möglichkeiten sind riesig und die Konstruktion mit Hilfe von Aluprofilen und Holz/PE Platten sehr einfach.
Vielleicht will ich auch zu viel oder denke zu kompliziert.
Daher ist Eurer Feedback gefragt und natürlich auch Eure Hilfe.
Da meine Zeichenkünste zu Wünschen Übrig lassen habe ich etwas gebastelt. Nur damit man erkennt worum es geht.
Ich versuche mich an Fusion 360, allerdings ist die Zeit immer sehr begrenzt um sich das alles selbst anzueignen.
Vielleicht haben ja einige von Euch Lust auf eine kleine Konstruktionskonferenz
(z.B.via Skype) wo man an ein paar Ideen und dem Konzept feilt und jemand mit Erfahrung bei Fusion360 zeigt wie man das ganze mit dem Programm umsetzt.
Ich hoffe es finden sich einige die Interesse drauf haben und helfen.
Wir haben ja ein sehr flexibles Software/Hardware System, nur das Chassis System ist sehr unflexibel und kaum modifizierbar.
Meine Überlegung geht in Richtung eines Dualen Systems mit verschiedenen Kombinationsmöglichkeiten.
Dabei gibt es einmal die Technik/Antriebssektion und die Nutzungssektion. (Mir fällt gerade kein besseres Wort ein)
In der Technik Sektion sind die Antriebe (36/42er Getriebemotoren, Brushless/Brushed ) Akkus (1 oder 2) und die Elektronik verbaut.
Neben dem Ardumower Mainboard muss der Platz ausreichend für ein paar Extras sein. (RaspberryPI, BMS, GPS....)
Die Nutzungssektion kann an die Technik Sektion gekoppelt werden und ist je nach Wunsch in Verschiedenen Ausführungen erhältlich.
Das heißt zum Beispiel
-mit einer oder zwei Mähscheiben Ausgestattet
-mit einer Transportplattform (z.B. für eine Mörtelwanne als Elektrische Schubkarre)
-mit einem Sitz und Lenksystem als kleines Elektro-Kettcar für Kinder
-mit einer Schneewalze
-mit einem Streuwagen für Dünger
Die Möglichkeiten sind riesig und die Konstruktion mit Hilfe von Aluprofilen und Holz/PE Platten sehr einfach.
Vielleicht will ich auch zu viel oder denke zu kompliziert.
Daher ist Eurer Feedback gefragt und natürlich auch Eure Hilfe.
Da meine Zeichenkünste zu Wünschen Übrig lassen habe ich etwas gebastelt. Nur damit man erkennt worum es geht.
Ich versuche mich an Fusion 360, allerdings ist die Zeit immer sehr begrenzt um sich das alles selbst anzueignen.
Vielleicht haben ja einige von Euch Lust auf eine kleine Konstruktionskonferenz
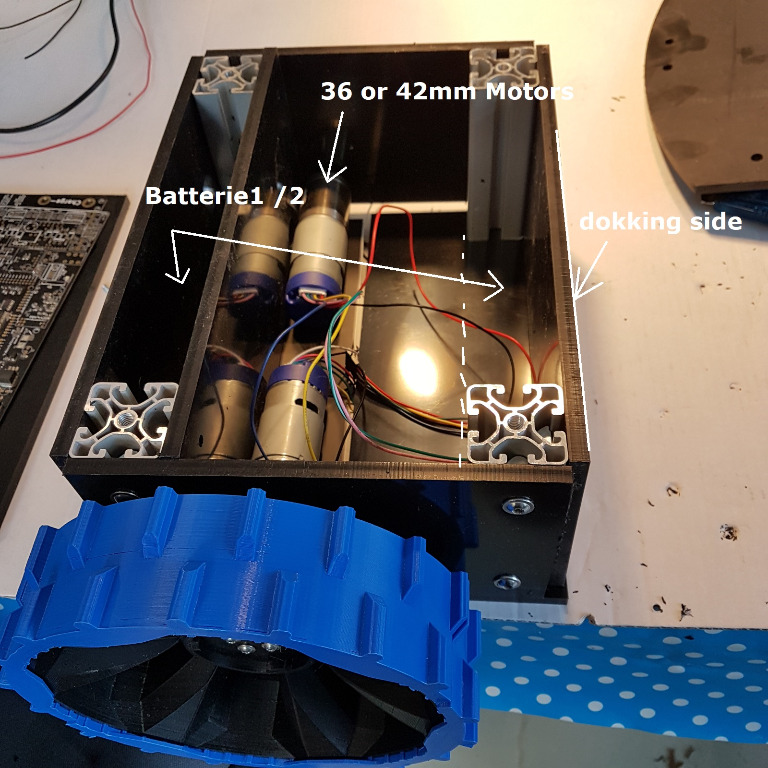
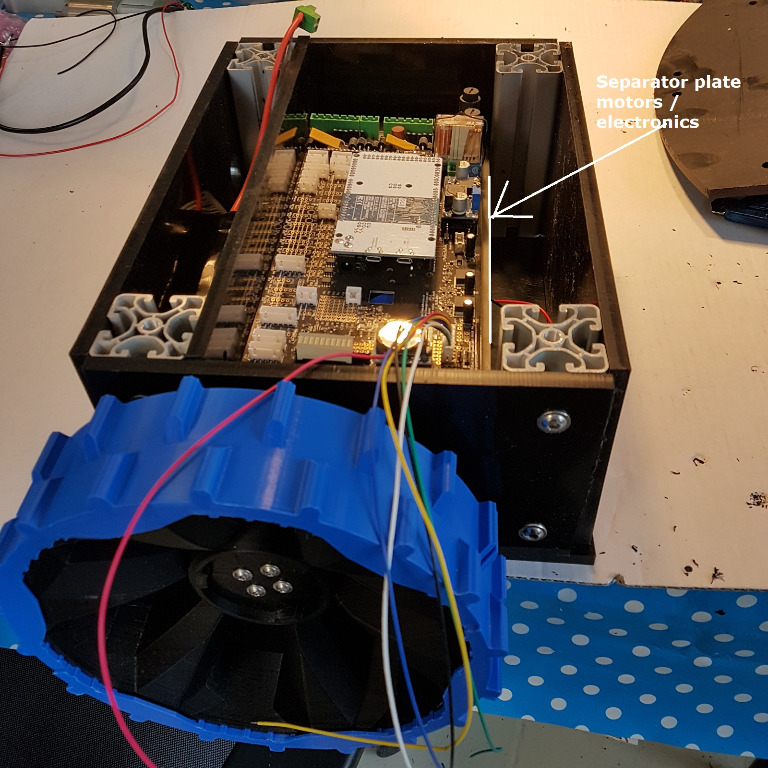
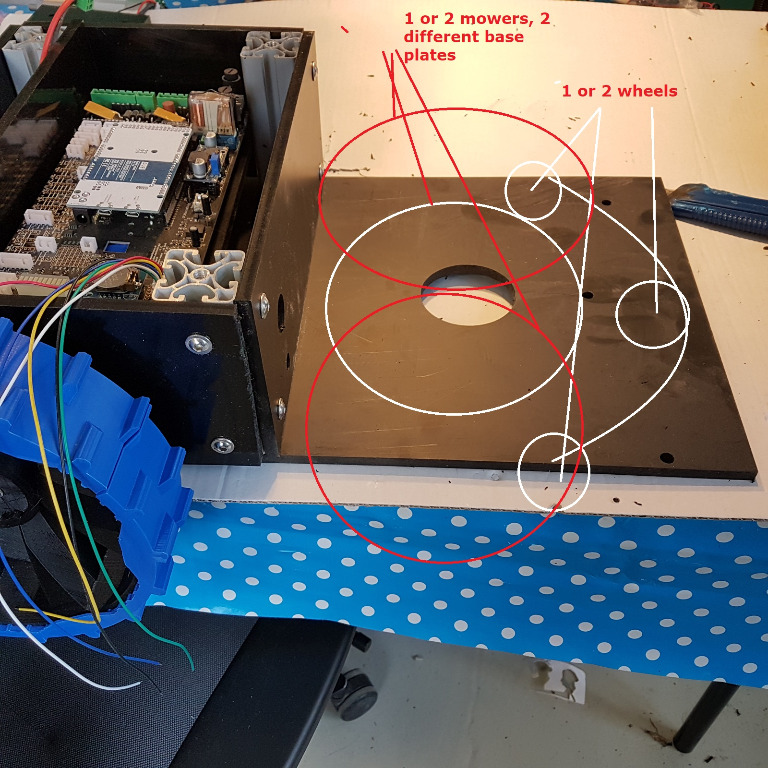
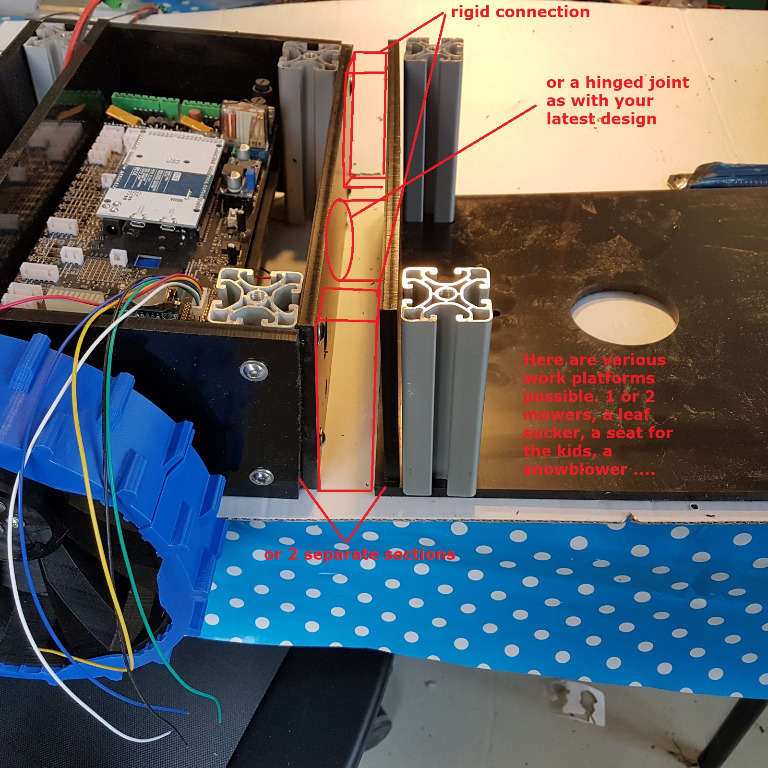